Welding technology or techniques
Arc welding process
Welding is a process of joining two or more pieces of metal by producing a localized union through fusion. The mandatory requirements for the union through fusion are:
- Clean the metallic surface
- Heat for raising the temperature of the local area to the melting point.
- The two metal to be joint do not have wide differential properties, such as aluminum and steel
Other optional requirements are:
- Filler metal - the purpose is to fill up the gap and this is not used in all fusion welding processes,e.g. no filler is used in resistance welding
- Pressure - this is used to bring the two surfaces close to each other.
- Deformation welding
- Diffusion welding
Deformation welding:-In this, two surfaces are brought close to very contact by applying high pressure which also deforms them. the surface temperature may or may not be very high e.g. Forge welding, Roll welding, Extrusion welding.
Diffusion welding:-Diffusion welding takes place by atomic diffusion between the two surfaces. The surfaces are usually heated to high temperature and pressure may be employed.
Brazing:-Brazing is also a process of joining of two metals. In this process, the two surfaces are to be joint not melted. Molten filler metal is used to fill up the gap. In than 450 deg. Celsius but less than that of either base metal. The filler metal is distributed between closed fit surfaces of joint by capillary action. e.g. by use of EutectRod 1801 to join copper to steel. Copper-based, silver-based alloys are most commonly used in brazing as filler material.
Braze welding:- It is a joining process like brazing where the filler metal melts but the base metal does not.The difference is, in braze welding, the filler metal is deposited in a groove and capillary action does not a factor.
Soldering:- Soldering is a process in which two metal pieces are joined together by melting or putting a filler metal into the joints, the filler metal having a lower melting point than the adjoining metal. In soldering the melting point of filler alloy is lesser than brazing, in soldering is less than 450 deg Celsius.
Fusion Welding (Electrical Energy)
Several processes are in the process by which fusion welding is carried out. Since the primary factor for welding is the source of heat by which the welding process is differentiated.
Processes may be:-
- MMAW (Manual Metal Arc Welding) or SMAW (Shield Metal Arc Welding)
- GTAW (Gas Tungsten Arc Welding) or TIG (Tungsten Inert Gas)
- GMAW (Gas Metal Arc Welding) or MIG (Metal Inert Gas)
- SAW (Submerged Arc Welding)
- FCAW (Flux Cored Arc Welding)
- Gas Welding
MMAW:-
Shield or Manual metal arc welding is a process, in which the heat for welding is generated by an electric arc, established between a flux covered consumable electrode and the workpiece. The electrode rod is made of a material that is compatible with the base material being welded and covered with a flux that gives off vapors that serve as a shielding gas, and provides a layer of slag both of which the protect the weld area by atmospheric contamination.
Advantages:-
- This is the simplest of all arc welding process.
- Portable
- Cost economical
- A big range of metals and their alloys can be welded.
- Welding can be carried out in any position.
- This process founds countless application.
GTAW (Gas Tungsten Arc Welding) or TIG (Tungsten Inert Gas) -
TIG is also an arc welding process in which a non-consumable tungsten electrode is used to produced weld. The weld area is protected from atmospheric contamination by inert shielding gas such as helium and argon, and filler metal is fed separately to weld. TIG is commonly used to weld a thin section of stainless steel and non-ferrous metal such as aluminum, magnesium, and copper alloy.
It is a relatively difficult welding method.
GTAW process normally requires two hands, since most application requires that the welder manually feed a filler metal into the weld area with one hand while manipulating the welding torch in other. Maintaining a short arc length while preventing contact between electrode and workpiece, is also important.
Once the arc is struck, welder moves the torch in a small circle to create a welding pool, the size of which depends on the size of the electrode and the amount of current. while maintaining a constant separation between the electrode and workpiece, the operator then moves the torch back slightly and tilts it backward about 10-15 degrees from vertical. Filler metal is added manually to the front end of the weld pool as it is needed.
GMAW OR MIG (Metal inert gas welding):
This process is known as MAG (Metal active gas welding).
Along with the wire a shielding gas also feeds through the welding torch to protect the weld pool from atmospheric contamination.
This process can be automatic or semi-automatic.
MIG welding can be used to weld steels, aluminum alloys, copper alloys(not with high zinc), magnesium alloys. It is suitable for position welding but works best in a down hand position.
The deposit efficiency is much higher than in manual arc welding with a very small amount of slag.
MIG Welding, however, requires a more expensive power source than MMAW. Normally a constant voltage power source is used. The equipment is also less portable.
Since the welding gun has to be close to the job, the process is less adaptable than SMAW in difficult to reach access.
SAW (Submerged Arc Welding):-
This is an arc welding process in which the heat for welding is supplied by an arc developed between a consumable solid wire or flux-cored wire and the job. The arc is shielded by a layer of granular fusible flux which covers the molten weld metal and the base metal near the joint. The arc is submerged influx is not seen easily from outside.
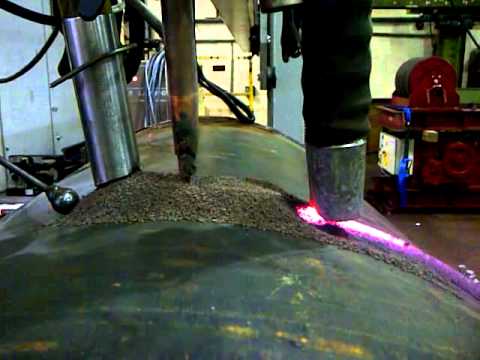
Submerged Arc Welding is either used in semi-automatic or fully automatic mode.
The process gives very high deposition rates (up to 40 kg/hr.) and can be used for welding very thick sections. It is used for both joining and overlaying. Due to the high current employed, the heat input is large and the flux cover gives a slow cooling rate. The combination of high heat input and low cooling rate makes this process more suitable for high hardenability metals like Ni-Hard than manual arc welding. As the flux is deposited in the granular form prior to arcing, SAW is suitable only for down hand welding.
SAW is also not suitable for welding plates less than 5mm in thickness as it might result in burn through.
FCAW (Flux-cored arc welding):-
In the FCAW where auxiliary shielding gases are used, shielding gases are normally CO or a mixture of argon and CO are used. The process becomes similar to GMAW (MIG) except that the electrode is tubular and not solid. Because of the flux in the electrode, more slag is present in FCAW as compared to GMAW but less than in SMAW.
FCAW with shielding gases gives radiography quality welds and can also be used for position welding if used with a small diameter electrode. The self-shielding FCAW requires a simpler welding torch and does not need a consumable inert gas. Since it is self-shielded, so it can be used in the outdoor process also. The quality weld made by this process is slightly inferior to that made by FCAW with auxiliary shielding gases like CO or Argon. That's why this process is not used for radiography welding quality.
FCAW process is faster than manual arc welding. Also the deposit efficiency is also much higher. One advantage of FCAW over GMAW is that Terocote deposit with high hardness etc. can be had with FCAW process. This cannot be achieved with a solid wire bare electrode.
Nice information about all type of welding
ReplyDeleteThanks for your valuable feed back
DeleteUseful post. This is my first time I visit here. I found so many intriguing stuff with regards to your blog particularly its conversation. Actually its incredible article. Keep it up. Mig welding accessories
ReplyDeleteI invite you to the page where you can read with interesting information on similar topics. find this
ReplyDeleteINFORMATIVE
ReplyDeleteGood information on blog. keep posting more.
ReplyDeleteBlack Wolf Plasma Torch in Ludhiana